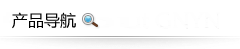
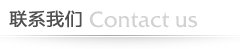
不銹鋼復(fù)合板的焊接缺陷和對策
發(fā)布日期:2014-07-30 15:17:00
熱裂紋
可分為凝固、液化、高溫失塑三大類。凝固裂紋多發(fā)生在焊縫區(qū);液化裂紋多出現(xiàn)在靠近熔合線的近縫區(qū),多層多道焊縫中層道間也可能出現(xiàn);高溫失塑裂紋通常發(fā)生在焊縫金屬凝固結(jié)晶完了的高溫區(qū)。
裂紋類型 形成時間 基本特征 被焊材料 分布部位及裂紋走向
熱裂紋 結(jié)晶裂紋(凝固裂紋) 在固相線溫度以上稍高的溫度,凝固前固液狀態(tài)下 沿晶間開裂,晶界有液膜,開口裂紋斷口有氧化色彩 雜質(zhì)較多的碳鋼、低中合金鋼、奧氏體鋼、鎳基合金及鋁 在焊縫中,沿縱向軸向分布,沿晶界方向呈人字形,在弧坑中沿各方向或呈星形,裂紋走向沿奧氏體晶界開裂
液化裂紋 固相線以下稍低溫度,也可為結(jié)晶裂紋的延續(xù) 沿晶間開裂,晶間有液化,斷口有共晶凝固現(xiàn)象 含S、P、C較多的鎳鉻高強(qiáng)鋼、奧氏體鋼、鎳基合金 熱影響區(qū)粗大奧氏體晶粒的晶界,在熔合區(qū)中發(fā)展,多層焊的前一層焊縫中,沿晶界開裂
失延裂紋及多邊化裂紋 再結(jié)晶溫度TR附近 表面較平整,有塑性變形痕跡,沿奧氏體晶界形成和擴(kuò)展,無液膜 純金屬及單相奧氏體合金 純金屬或單相合金焊縫中,少量在熱影響區(qū),多層焊前一層焊縫中,沿奧氏體晶界開裂
產(chǎn)生基本原因:
導(dǎo)熱系數(shù)小、線膨脹系數(shù)大,焊接接頭高溫停留時間較長,焊縫金屬及近縫區(qū)在高溫承受較高的拉伸應(yīng)力與拉伸應(yīng)變。
在焊縫中聯(lián)生結(jié)晶形成方向性很強(qiáng)的粗大柱狀晶組織,在凝固結(jié)晶過程中,一些雜質(zhì)元素及合金元素,如S、P、Sn、Sb、Si、B、Nb易于在晶間形成低熔點的液態(tài)膜,因此造成焊接凝固裂紋;對于奧氏體不銹鋼母材,當(dāng)上述雜質(zhì)元素的含量較高時,將易產(chǎn)生近縫區(qū)的液化裂紋。
高溫凝固模式和高溫結(jié)晶組織對熱裂紋敏感性的影響。當(dāng)奧氏體的室溫組織中含有少量的δ鐵素體時(3%~12%),其熱裂紋敏感性顯著降低。凝固模式有:A;AF;FA。A模式熱裂紋敏感性較高(根據(jù)晶粒潤濕理論,在結(jié)晶過程中形成的依棉液態(tài)膜能夠潤濕γ界面,而難以潤濕γ-δ界面,因此A模式形成的的純奧氏體組織具有較高的熱裂紋敏感性);FA模式抗熱裂紋性能優(yōu)良(先析出的鐵素體打亂了奧氏體柱狀晶的方向,而且形成了偏析液態(tài)膜難以潤濕γ-δ界面,因此具有優(yōu)良的抗熱裂紋性能。與此同時,先析δ鐵系體還能較高地溶解S、P、Sn等雜質(zhì),降低了凝固液體中的雜質(zhì)含量,進(jìn)而提高了抗熱裂紋的性能。以AF凝固模式形成的奧氏體+鐵素體組織,鐵素體在凝固結(jié)晶的后期產(chǎn)生,可以阻止粗大奧氏體柱狀晶的長大,有分隔殘液的作用,同時也可較多溶解雜質(zhì)元素,因此此模式形成的A+F組織也具有低的熱裂紋敏感性。
除其他因素外,鐵素體含量與焊縫金屬成分存在一定關(guān)系。鐵素體含量可以通過調(diào)整鐵素體形成元素(如Cr、Si、V、Ti、Mo)與奧氏體形成元素(如C、Ni、N)的比率來確定。
1)鐵素體的作用
在奧氏體不銹鋼焊件中,鐵素體最重要的作用是降低某些不銹鋼焊縫的熱裂紋傾向。
鐵素體含量的下限要求對于避免產(chǎn)生裂紋是必要的,當(dāng)?shù)腿垭s質(zhì)元素(特別是硫、磷)含量很低時,奧氏體不銹鋼焊縫金屬抗熱裂紋性能有所提高。通常熱裂紋受凝固模式影響。最終的鐵素體含量和形式取決于結(jié)晶過程和隨后的固體狀態(tài)。熱裂紋的敏感性按照以下凝固模式的順序降低:單相奧氏體、初生奧氏體、混合型和單相鐵素體、初生鐵素體。雖然鐵素體和凝固模式都主要取決于化學(xué)成分。在FA凝固模式下,初始鐵素體向奧氏體轉(zhuǎn)變,產(chǎn)生雙相組織,大大增加了相的邊界數(shù)量,在此邊界可能分布有低熔點組合物,從而使焊縫金屬中微裂的可能進(jìn)一步減小。至少要3FN(鐵素體數(shù)為3)的δ鐵素體含量可消除用E308、E308L、E316、E316L奧氏體填充金屬所熔敷的焊縫金屬中的微裂。E309中需要4FN,E318中為5FN,在E347中為6FN。
鐵素體含量超過一定限制,可能會降低力學(xué)性能。為了控制熱脆性,要求焊縫金屬中的δ鐵素體約為4~10%。過量的鐵素體在高溫下放置過程中可導(dǎo)致σ脆化。某些填充金屬可能得到太高的鐵素體含量,特別是高鉻低鎳型,312型。
鐵素體含量超過一定限制,可能會降低某些焊縫熔敷層在熱的、氧化性酸中的耐腐蝕性能。添加鉬的18Cr-12Ni奧氏體填充金屬,如E316、E317、E318型,在焊態(tài)條件下對某些介質(zhì)的抗腐蝕性能不好。存在局限于對鐵素體的腐蝕時,可在焊后對接頭退火,或者是采用不產(chǎn)生鐵素體的焊縫金屬的成分。
2)成分和組織間的關(guān)系
焊縫中鐵素體含量一般用磁性檢測儀進(jìn)行測量,測量結(jié)果用鐵素體數(shù)(FN)表示。由于成分和組織是相關(guān)聯(lián)的,即鐵素體元素(鉻當(dāng)量)和奧氏體元素(鎳當(dāng)量),因此鐵素體含量也可以通過相圖進(jìn)行估算。為了將Cr-Ni奧氏體不銹鋼的化學(xué)成分與結(jié)晶模式及金相組織密切聯(lián)系起來,并用于評估焊縫金屬的熱裂紋敏感性,明確防止焊接熱裂紋的材料冶金措施,通過焊接時快速冷卻形成的不銹鋼的焊縫組織與合金元素的鉻當(dāng)量(Creq)和鎳當(dāng)量(Nieq)值的關(guān)系圖,可以看出,奧氏體不銹鋼及其焊縫金屬,當(dāng)室溫組織中含有少量的δ鐵素體時(4%~12%),其凝固模式基本為FA,能有效防止焊接熱裂紋。
熔敷狀態(tài)下焊縫金屬的顯微組織取決于它的成分和結(jié)晶速度。碳和氮在穩(wěn)定奧氏體作用中的有效性各比鎳大約30倍,添加少量的鈦可以提高熔敷金屬鐵素體含量達(dá)幾個鐵素體數(shù)。
3)焊接條件的影響
焊縫金屬的鐵素體含量由焊縫金屬化學(xué)成分的決定,它主要受焊接材料、母材的稀釋、焊接條件影響;瘜W(xué)成分中影響最大的是氮和氮,氮和鉻的改變可明顯影響鐵素體含量。高電弧電壓(電弧過長)可造成焊縫金屬氮污染,并且造成鉻氧化損失,使焊縫中鐵素體含量遠(yuǎn)低于規(guī)定值。其他的因素是通過藥皮中的氧化物減少鉻含量(可用Nb、Ti除氧穩(wěn)定),或者是從二氧化碳中增加碳含量。很高的熱輸入也可以產(chǎn)生一定的影響,特別是對雙相鋼的影響。
當(dāng)未經(jīng)稀釋的焊縫金屬中的鐵素體含量與制造廠出具的質(zhì)量證明不相符時,可能是由上述中的一種或者多種因素造成的。
一般要求母材稀釋率低于40%。受母材稀釋高的焊道可能已改變了鐵素體含量,從一焊縫到另一焊縫,以及在同一焊縫中從根部到表面就可能存在鐵素體含量的顯著差別。要特別注意根部焊道中對稀釋的影響。如產(chǎn)品管了焊縫中,按工藝合格值檢查全部焊縫,近50%至少相差2FN。因為在母材和填充金屬之間標(biāo)稱成分上一般是有差別的,熔深和焊道形狀的輕微變化,使稀釋率變化,可以使熔敷金屬的成分和性能產(chǎn)生明顯的變化。
熔敷金屬中鐵素體含量隨著:
(1).電弧電壓的升高(拉長電弧)而急劇下降。焊接電壓是影響鐵素體含量的主要因素。(N和Cr的影響)
(2).隨著焊接電流的提高而降低。
(3).隨著冷卻速度的加快而有所提高,隨著層間溫度的升高而有所降低。
(4).焊接角度對熔敷金屬中鐵素體含量有一定影響。
4)熱處理的影響
固溶處理能顯著減少鐵素體含量。
5)焊接熱裂紋的控制
主要從控制焊縫金屬成分和調(diào)整焊接工藝兩方面進(jìn)行控制。
1).控制焊縫金屬成分
其中最關(guān)鍵的是針對某一成分母材,選擇合適的焊接材料,防止裂紋產(chǎn)生。
(1).成分控制中還有一個極為重要的問題是限制有害雜質(zhì)的含量。對于各種材料,均需嚴(yán)格限制硫、磷含量,同時適當(dāng)提高ω(Mn)/ω(S)或ω(Mn)3/ω(S)的比值。
(2).結(jié)構(gòu)鋼焊縫中的ω(C)最好限制小于0.10%,不要超過0.12%。由于磷難以用冶金反應(yīng)來控制,只能限制其來源。
(3).對于不同材料,還有些各不相同的有害雜質(zhì)。例如,對單相γ的奧氏體鋼或合金的焊縫金屬,硅是非常有害的雜質(zhì),鈮也促使熱裂,因為硅與鈮均可形成低熔點共晶。但在γ+δ雙相焊縫中,硅或鈮作為鐵素體化元素,反而有利于改善抗裂性。單相奧氏體鋼的焊縫中的錳可改善抗裂性,但有銅存在時,錳與銅相互促使偏析加強(qiáng),大大增加結(jié)晶裂紋傾向。
2).調(diào)整焊接工藝
(1).限制熔池過熱。過熱易促使熱裂,應(yīng)降低熱輸入。小線能量能減小晶粒度和降低應(yīng)變量,減小結(jié)晶裂紋傾向,同時縮小固相近縫區(qū)的熱裂敏感區(qū)CSZ的大小,從而減小整個焊接接頭熱裂傾向。
(2).控制成形系數(shù)。焊縫成形系數(shù)越小,熱裂紋傾向越。ㄅc低合金鋼相反)。凸面焊縫比凹面焊縫熱裂紋傾向小,但不能避免在焊根出現(xiàn)裂紋的可能。“梨形”斷面焊道中易產(chǎn)生熱裂紋。
(3).降低焊接電流,減小熔合比。
(4).控制裝配間隙、改進(jìn)裝配質(zhì)量,降低拘束度。
3.1.3.2焊縫金屬的低溫脆化
為了滿足低溫韌性的要求,焊縫組織通常希望獲得單一的奧氏體組織,避免δ鐵素體的存在,而惡化低溫韌性。
3.1.3.3 475℃脆性(σ相脆化)
475℃脆性指鉻的質(zhì)量分?jǐn)?shù)大于15%并含有較多鐵素體相的不銹鋼,在350~550℃溫度范圍內(nèi)長時間停留或緩冷出現(xiàn)的一種脆化現(xiàn)象,并使鋼的強(qiáng)度、硬度顯著提高,由于這種脆化現(xiàn)象在475℃左右最敏感,故稱475℃脆性。475℃脆性主要發(fā)生在高鉻鐵素體鋼、含較多鐵素體的奧氏體不銹鋼,及其焊縫中,含鐵素體越多,脆化傾向越嚴(yán)重。發(fā)生475℃脆性后,可以通過重新加熱至590~650℃,保溫1~5h后快冷予以消除。
σ相是一種無磁且具有高硬度的脆性富鉻金屬間化合物,σ相的名義成分是Fe、Cr,但實際上由于Ni、Mo等原子參與析出,該相的實際成分應(yīng)為(FeNi)x(CrMo)y。鉻與鐵的質(zhì)量分?jǐn)?shù)分別達(dá)到80%和20%,主要析集于柱狀晶的晶界,含Cr量可高達(dá)61%~82%,含鐵量為37%~17.5%,尺寸為10~20nm,此相具有體心立方結(jié)構(gòu)且無磁性,晶格常數(shù)為0.2877nm,介于鐵與鉻的晶格常數(shù)之間。由于σ相富Cr,還會富Mo、Si,因而在其周圍常常會出現(xiàn)貧Cr(或MO、Si)區(qū),或由于σ相本身的選擇性溶解而降低鋼的耐蝕性。
在奧氏體焊縫中,γ相δ相均可發(fā)生σ相轉(zhuǎn)變,當(dāng)δ鐵素體含量超過12%時,δ→σ的轉(zhuǎn)變將非常顯著,造成焊縫金屬的明顯脆化。σ相析出的脆化還與奧氏體不銹鋼中合金化程度相關(guān),Cr、Mo具有明顯的σ化作用,而Cr、Mo等合金元素含量較高的超級奧氏體不銹鋼,易析出σ相。提高奧氏體化合金元素Ni含量,防止Ni在焊接過程中的降低,可有效抑制它們的σ化作用,是防止焊接接頭脆化的有效冶金措施。
產(chǎn)生475℃脆性的原因是σ相的析出。該富鉻相在母相晶面族上及位錯處的析出且與母相仍保持共格關(guān)系,導(dǎo)致發(fā)生晶格畸變,產(chǎn)生很大的內(nèi)應(yīng)力使滑移堆以進(jìn)行,易于產(chǎn)生孿晶。孿晶面會形成解理斷裂的形核點,從而導(dǎo)致脆化,使常溫及負(fù)溫時的沖擊初度嚴(yán)重下降(高溫時不降),并使鋼的耐蝕性顯著降低。下圖是Fe-Cr合金中σ相存在的相圖,從相圖中可以看出,σ相的產(chǎn)生是由于520℃以下σ→α+σ反應(yīng)的結(jié)果。由于σ相析出較為緩慢,因此,從σ相在α相的溶解度線以上加熱所得到的單相α,即使在空冷的條件下,也不會有σ相的析出。只有在520℃以下長時間保溫,σ相才會析出,從而導(dǎo)致鋼的脆化。一般來說,不銹鋼σ相經(jīng)過固溶處理,或加熱到σ相形成溫度(550℃以上)以上保溫一段時間,使σ相溶解到基體中,然后快冷卻,可以有效地防止σ相析出,使鋼的塑性、韌性得到恢復(fù)。一般認(rèn)為σ相直接產(chǎn)生于鐵素體相,則鐵素體形成元素會促進(jìn)鐵素體含量增加,也就促進(jìn)σ相析出,也就增加475℃脆性的敏感性。
3.1.3.5均勻(表面)腐蝕
耐酸鉻不銹鋼的最低含鉻為12.5%,如要求抗高濃度酸的腐蝕則必需使鉻含量達(dá)到第二個相應(yīng)突變值,即鉻的摩爾分?jǐn)?shù)為25%或更高。
鉻不銹鋼在氧化性介質(zhì)中容易先在表面形成富鉻氧化膜的鈍化作用,對氧化性酸、大氣有較好耐均勻腐蝕性,但對非氧化性酸(稀硫酸、醋酸)的耐腐蝕性不好。
3.1.3.6晶間腐蝕
根據(jù)不銹鋼及其焊縫金屬化學(xué)成分、所采用的焊接工藝方法,焊接接頭可能在三個部位出現(xiàn)晶間腐蝕,包括焊縫的晶間腐蝕、緊靠熔合線的過熱區(qū)“刀蝕”及熱影響區(qū)敏化溫度區(qū)的晶間腐蝕。對于焊縫金屬,根據(jù)貧鉻理論,在晶界上析出碳化鉻,造成貧鉻的晶界是晶間腐蝕的主要原因。
在腐蝕介質(zhì)中,導(dǎo)致晶間腐蝕的原因:
1)碳化鉻析出:在500~800℃溫度區(qū)間敏化時,過飽和固溶的碳向晶粒間界的擴(kuò)散比鉻的擴(kuò)散的快,在晶界附近和鉻結(jié)合成(Cr、Fe)23C6的碳化物并在晶界沉淀析出,形成了晶粒邊界附近區(qū)域的貧鉻現(xiàn)象。當(dāng)該區(qū)鉻含量降低到鈍化所需的極限[ω(Cr=12.5%)]以下時,在腐蝕環(huán)境中就會加速該區(qū)發(fā)生晶間腐蝕。熔化焊接時,熔合線附近由于過熱,大部分碳化物被溶解。當(dāng)?shù)诙渭訜岬矫艋瘻囟葏^(qū)(或多層焊或熱處理)時,主要沿晶界析出了鉻的碳化物,由此引起晶間腐蝕。防止措施:采用超低碳[ω(C<0.03%)以下或更低]或加Ti、Nb等穩(wěn)定化元素[Nb或Ti的質(zhì)量分?jǐn)?shù)為(8~10)ω(C)~1.0%]的母材和填充金屬;調(diào)整相比例,使之含有4%~12%的δ鐵素體;固溶處理(1010~1120℃);采用穩(wěn)定化處理使晶內(nèi)鉻擴(kuò)散均勻化以消除局部貧鉻現(xiàn)象;焊接采用較小的焊接熱輸入,加快冷卻速度。
2)σ相析出:某些超低碳含鉬奧氏體不銹鋼,如316L在敏化溫度區(qū)間在晶界析出σ相,在沸騰的65%硝酸溶液中可發(fā)現(xiàn),σ相析出引起的晶間腐蝕。
3)晶界吸附:不銹鋼中雜質(zhì)P在晶界吸附是引起硝酸溶液中產(chǎn)生晶間腐蝕的原因。
4)穩(wěn)定化元素高溫溶解:含鈦和含鈮奧氏體不銹鋼焊后在敏化溫度加熱處理,再放入強(qiáng)氧化性的硝酸溶液中工作,將在熔合線上出現(xiàn)很窄區(qū)域的選擇性腐蝕,常稱為“刀狀腐蝕”。
3.1.3.7點蝕及縫隙腐蝕
由腐蝕區(qū)產(chǎn)生“閉塞電池腐蝕”(OCC)作用所致。由于材料表面鈍化膜的局部破壞引起。材料Ea值越正(陽極電位越高),耐點蝕能力越好:介質(zhì)中,CL-的濃度越低,越不容易引起點蝕;增加材料的均勻性,即減少夾雜物(特別是硫夾雜物)、晶界析出物(晶間碳化物或σ相等)以及提高鈍化膜的穩(wěn)定性,如降低碳含量,增加鉻和鉬以及鎳含量等都能提高抗點蝕力,F(xiàn)在超低碳高鉻鎳含鉬奧氏體不銹鋼有較高的耐點蝕性能。
由于連接處的縫隙被腐蝕產(chǎn)物覆蓋以及介質(zhì)擴(kuò)散受到限制等原因,該處的介質(zhì)成分和濃度與整體有很大差別,形成了“閉塞電池腐蝕”的作用。和點蝕形成機(jī)理有差異之點在于縫隙腐蝕主要是介質(zhì)的電化學(xué)不均勻引起的。
3.1.3.8應(yīng)力腐蝕斷裂(SCC)
在一定靜拉伸應(yīng)力與一定溫度條件下的特定電化學(xué)介質(zhì)共同作用下,因陽極溶解過程引起的斷裂。分為應(yīng)力腐蝕、氫脆和腐蝕疲勞。氫脆是在靜拉力與電化學(xué)介質(zhì)作用下,由于陰極吸氫而引起斷裂。腐蝕疲勞的應(yīng)力,不僅是靜拉應(yīng)力,更主要地是交變的周期性的拉-拉、拉-壓的動態(tài)應(yīng)力。產(chǎn)生因素:冷熱加工產(chǎn)生的殘余拉應(yīng)力、焊接接頭的組織變化、酸洗處理不當(dāng)、在母材上隨意打弧、焊接接頭設(shè)計不合理造成應(yīng)力集中、腐蝕介質(zhì)的局部濃度提高等。
特定條件如下:
1)介質(zhì)條件。腐蝕介質(zhì)與材料的組合上有選擇性。奧氏體不銹鋼的介質(zhì)因素,主要是溶液中CL-離子的濃度和氧含量的關(guān)系。CL-離子和O2兩者共存并且濃度與量都較高時,才會產(chǎn)生應(yīng)力腐蝕,這種現(xiàn)象常稱為氧脆。溫度多在50℃以上。結(jié)構(gòu)中縫隙以及流動性不良等引起介質(zhì)濃縮部位均發(fā)生應(yīng)力腐蝕斷裂。
2)應(yīng)力條件。在拉應(yīng)力作用下才能產(chǎn)生。主要是冷、熱加工過程中的殘余應(yīng)力,所以消除殘余應(yīng)力是防止應(yīng)力腐蝕最有效措施之一。合理設(shè)計焊接接頭,避免腐蝕介質(zhì)在焊接接頭部位聚集,降低或消除焊接接頭的應(yīng)力集中。盡量降低焊接殘余應(yīng)力,在工藝方法上合理布置焊道順序,如采用分段退步焊。采取一些消應(yīng)力措施,如焊后完全退火、焊后錘擊或噴丸等。
3)材料條件。一般純金屬不產(chǎn)生應(yīng)力腐蝕,均發(fā)生在合金中。在晶界上的合金元素偏析是引起合金的晶間型開裂的應(yīng)力腐蝕的重要原因。一般提高晶體堆垛層錯能的元素(如Ni、C)能提高奧氏體不銹鋼應(yīng)力腐蝕能力,降低堆垛層錯能的元素(如Nb、Ti、Mo、N)容易引起應(yīng)力腐蝕。在奧氏體鋼中增加鐵素體含量時,也能增加抗應(yīng)力腐蝕的能力,當(dāng)鐵素體超過60%時,又有所下降。合理選擇母材與焊接材料,如在高濃度氯化物介質(zhì)中,超級奧氏體不銹鋼就顯示出明顯的耐應(yīng)力腐蝕能力。在選擇焊接材料時,為了保證焊縫金屬的耐應(yīng)力腐蝕性能,通常采用超合金化的焊接材料,即焊縫金屬中的耐蝕合金元素(Cr、Mo、Ni等)含量高于母材。
4)表面質(zhì)量。采用合理工藝方法保證焊接接頭部位光滑潔凈,焊接飛濺物,電弧擦傷等往往是腐蝕開始的部位,也是導(dǎo)致應(yīng)力腐蝕發(fā)生的根源,因此,焊接接頭的外在質(zhì)量也是至關(guān)重要。
斷裂部位和形貌特征:一般出現(xiàn)在近介質(zhì)表面,從表面開始向內(nèi)部擴(kuò)展,點蝕是裂紋的根源,一般沒有總體均勻腐蝕。裂紋通常表現(xiàn)為穿晶擴(kuò)展,裂紋整體為樹枝狀,宏觀裂紋較平直,常常有分枝、花紋和龜裂。微觀裂紋一般有分枝特征,裂紋尖端較銳利,根部較寬,且常起源于點蝕坑底和表面,有沿晶、穿晶與混合型的裂紋。斷口形貌一般無顯著的塑性變形,宏觀斷口粗糙,多呈結(jié)晶狀、層片狀、放射狀和山口形貌。微觀斷口穿晶型為準(zhǔn)解理斷裂、有河流(河川)花樣、山形、扇形花樣、魚骨狀花樣、羽毛狀花樣、流水狀花樣、及伴有腐蝕產(chǎn)物的泥狀龜裂花樣以及石塊狀堆積花樣等,有撕裂嶺,有二次裂紋或表面蝕坑。沿晶型呈冰糖塊狀花樣。